The platform of USA 17 arrived on January 30th and by February 20th we had the boat assembled and the hardware in place. Chris, our exhibit production manager, had designed, and Hampton Sheet Metal had constructed the four platforms that would support the boat in the gallery. But we had one little problem—well, it wasn’t little, it was about a 6 ton problem—the platform was in the wrong position for the exhibition.
Knowing we would need to move the pieces of the platform around after they were in the gallery we purchased four 3,600lb Yardarm dollies (these are V-shaped adjustable dollies for boats). We worked with Hampton Roads Crane and Rigging to seat the hulls on the dollies as we put the hulls in the gallery (we located them under or near bulkheads to make sure they provided good support and wouldn’t damage the boat). It made moving the hulls around a breeze during the assembly process, but we weren’t sure how easy it would be to move the entire platform. So I did what I always do when I need to move a big boat—I put out an all call to the Museum staff.
At 1:00 the day before the scheduled lift, about 30 or so staff showed up to help us move the platform. And unlike Oracle’s shore team, many of our boat movers were wearing high heels! Chris and I had so much help that the move went flawlessly and only took about two minutes to complete (most of that was me talking to make sure the staff understood what we had to do, where to support the boat, and any problems we might encounter). The video is a little long (almost three minutes) as my video editing skills aren’t great, but it is totally worth watching.
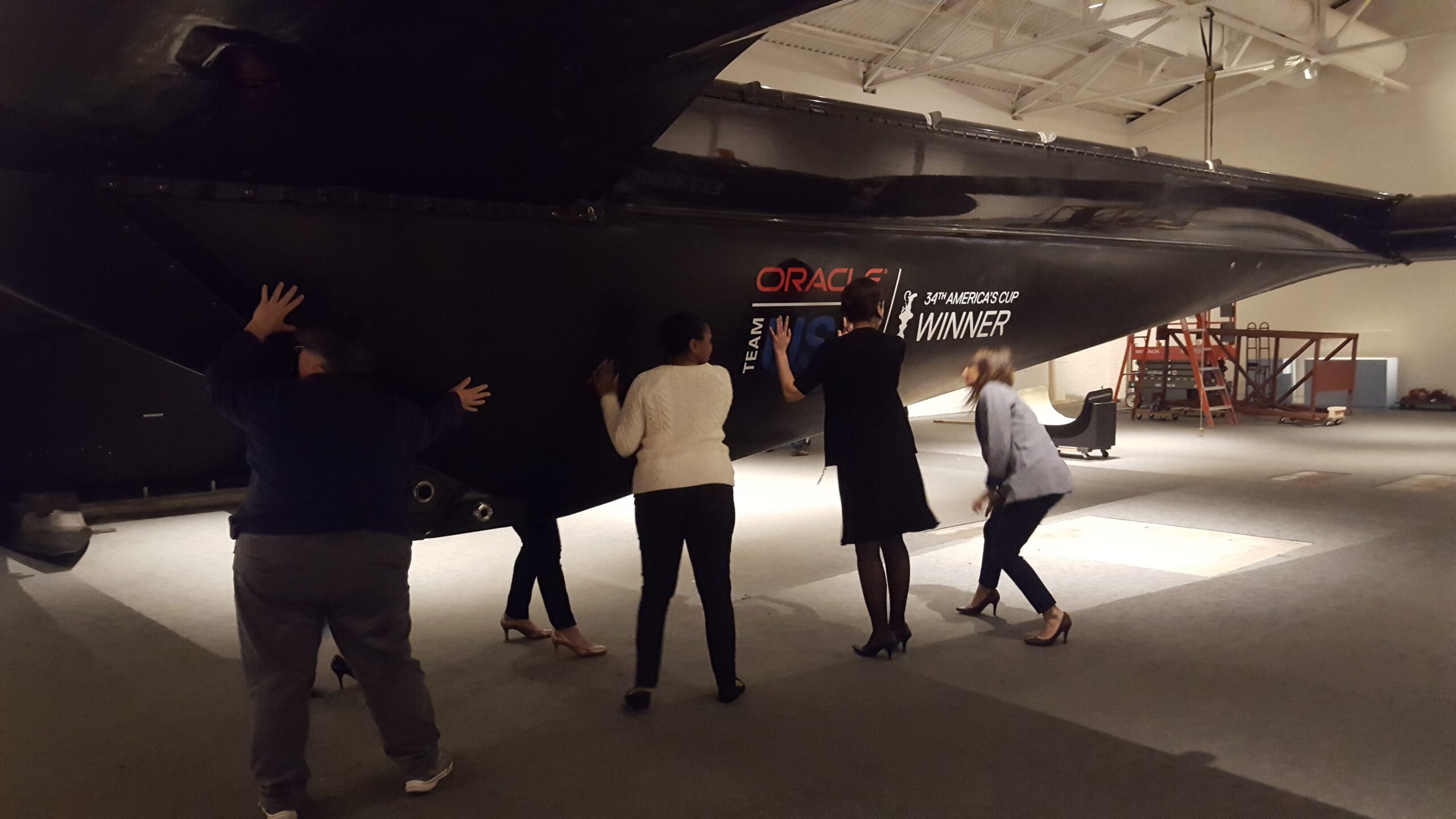